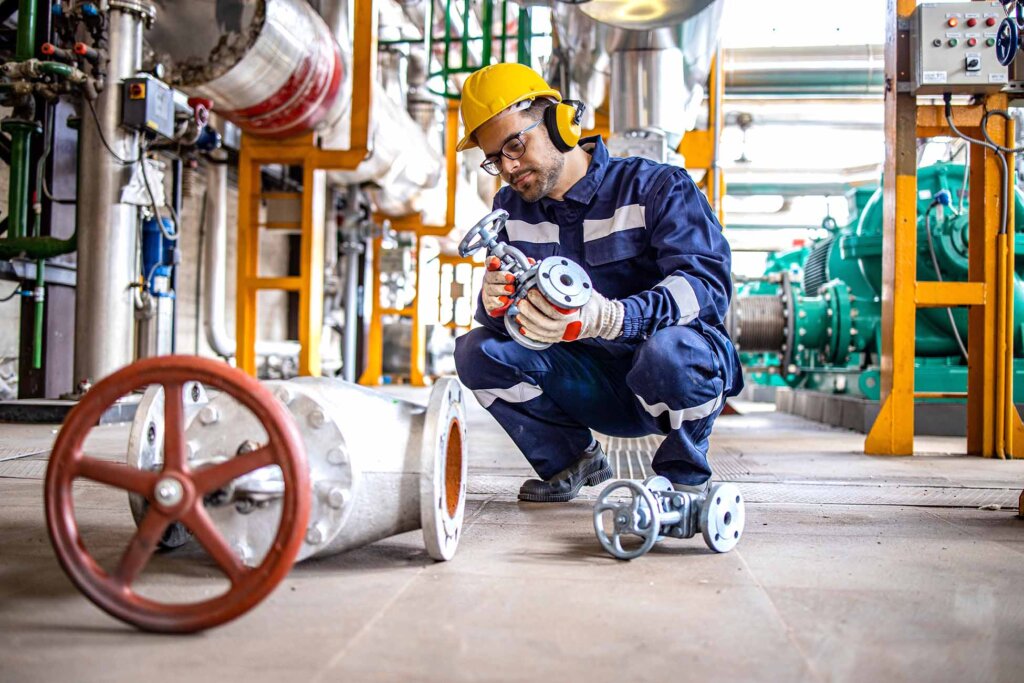
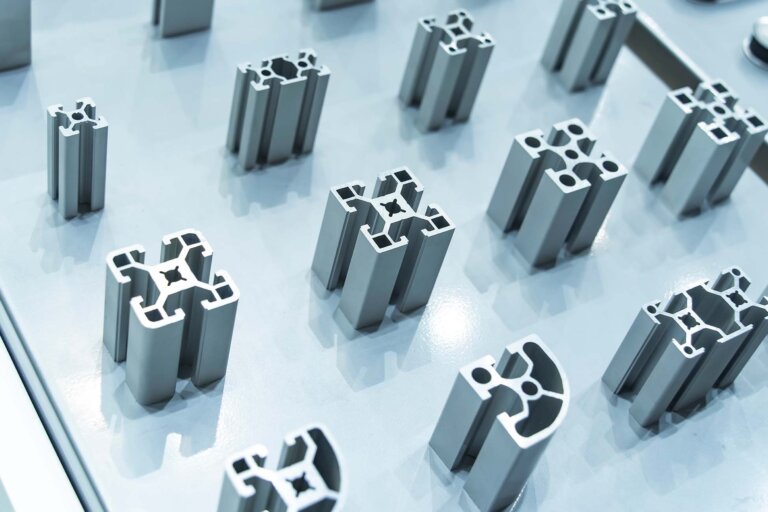
Understanding Extrusion: A Fundamental Manufacturing Process
In the world of manufacturing, where innovation and efficiency reign supreme, various techniques and processes have evolved to meet the demands of diverse industries. Among these, extrusion stands out as a fundamental and versatile method used in the production of numerous everyday items, from pipes and tubing to food products and even 3D printing filaments.
But what exactly is extrusion, and how does it impact our daily lives?
Table of Contents
What Is an Extrusion?
At its core, extrusion is a manufacturing process that involves shaping raw materials into a desired cross-sectional profile through a die. This technique extends to metals, ceramics, and food products, making it a ubiquitous method across various industries.
Components of the Extrusion Process
Extrusion equipment typically comprises a few essential components:
- Extruder: The heart of the extrusion process, the extruder is a machine that houses a screw or a ram to transport the raw material through the system. It applies heat and pressure to soften or melt the material for processing.
- Die: The die is a precision tool that shapes the material as it passes through, giving it the desired profile. The die shape is designed based on the product specifications.
- Cooling System: Following the shaping process, a cooling system helps solidify the material into its final form. This can involve water baths, air cooling, or other methods, depending on the material being extruded.
What Is the Extrusion Process?
The extrusion process involves the application of heat and pressure to force the material, usually in a molten or semi-solid state, through a specifically designed opening—a die shape—with the desired cross-sectional profile. The material emerges on the other side of the die in the shape required for its final application.
Variants of the Extrusion Process
There are various types of extrusion processes, each suited for different materials and end products. These processes include direct extrusion, indirect extrusion, cold extrusion, and hot extrusion.
- Direct Extrusion: Also known as forward extrusion, this involves pushing the material through the die in a continuous process. It’s common in the creation of solid shapes like rods or bars.
- Indirect Extrusion: In contrast, indirect extrusion involves the die moving with the ram, reducing friction and allowing for more complex shapes to be formed.
- Cold Extrusion: This process is conducted at or near room temperature, ideal for materials that might lose their properties under heat. Cold extrusion is perfect for products that require high strength or close tolerances.
- Hot Extrusion: Often used for metals and thermoplastics, hot extrusion involves heating the material to make it more malleable, aiding the extrusion process. Not to be confused with warm extrusion, the hot extrusion process takes place at a much higher temperature.
Commonly Extruded Materials
Extrusion is a versatile manufacturing process used with a wide range of materials. The most common extruded materials include softer metals, plastic materials, and food products, each serving specific industries and applications. The Federal Group specializes in the following metal materials for the extrusion process:
- Aluminum
- Brass and Bronze
- Copper
- Steel
The raw material or stock material is typically handled as a cylindrical billet similar to the image above.
Applications of Extrusion
Metal extrusion has found widespread use in various industries, each harnessing its unique capabilities to meet specific needs. Even though it is commonly utilized as a metal forming process, plastic extrusion can create a variety of specialty plastic products like plastic pellets and rigid pvc. Let’s explore the different industries that rely on metal extrusions.
Construction Sector
In the construction sector, extrusion is crucial for creating materials like aluminum or steel beams, window frames, and even certain types of bricks or tiles. The ability to produce long, continuous sections of materials with specific cross-sectional profiles makes it an invaluable technique.
Consumer Goods Industry
Metal extrusions also find applications in the consumer goods industry for various products, including furniture frames, bicycle frames, and more. They are also commonly found in appliance components like ovens, fireplace frames, and ovens.
Electrical and Electronics Industry
Metal extrusion is used in the electrical and electronics industry to create heat sinks, enclosures, and conductive components.
Marine Industry
In the marine industry, metal extrusions are valued for their corrosion resistance and durability in harsh, saltwater environments. They are used for boat components, plumbing, ventilation systems, rails, cleats, and more.
Manufacturing and Industrial Equipment
The metal extrusion process plays a significant role in manufacturing and industrial equipment. Some of the products created by metal extrusion include conveyor systems, material handling systems, frames for mechanical equipment or machines, plus safety barriers and guardrails.
Advantages and Limitations of the Extrusion Process
Advantages of Extrusion
- Cost-Effectiveness: The extrusion process allows for continuous production, reducing the need for additional processing steps and lowering production costs.
- Efficiency and Precision: The process offers high precision and repeatability in creating complex shapes with consistent quality.
- Versatility: The extrusion process is versatile, accommodating a wide range of materials and enabling the production of various end products.
- Strength: In regard to metal extrusion, the mechanical properties of the alloy post-extrusion process have greater tensile strength.
Limitations of Extrusion
- Material Constraints: Not all materials are suitable for extrusion, particularly those that may degrade or lose properties under heat. In addition, softer metals are ideal for the metal extrusion process.
- Initial Setup Costs: Customizing dies and setting up extrusion processes can involve significant initial expenses.
Frequently Asked Questions
What is hydrostatic extrusion?
Hydrostatic extrusion is a metal forming process in which a billet is forced through a die by hydraulic pressure, resulting in precise and uniform deformation of the material. The hydrostatic extrusion process can take place in a warm, cold, or hot temperature.
What is friction extrusion?
Friction extrusion is a solid-state process that involves rotating a cylindrical tool within a stationary workpiece, generating heat through friction, and allowing the material to deform and flow plastically, resulting in the creation of complex shapes with reduced energy consumption. It is particularly useful for joining dissimilar materials and recycling scrap or waste materials into useful products.
What is impact extrusion?
The impact extrusion process involves a punch impacting a metal slug placed within a die, causing the material to flow and take the shape of the die cavity.
What is lateral extrusion?
The lateral extrusion process is just another form of extrusion where the container is in a vertical orientation. This process is utilized in the production of profiles, bars, and sections with precise dimensions, often in the construction, automotive, and manufacturing industries.
What is the difference between plastic injection molding and the extrusion process?
Plastic injection molding involves injecting plastic material into a mold cavity to create complex three-dimensional parts, while extrusion forces material through a die to produce shapes like pipes, tubing, and profiles. Per the name, plastic injection molding can only work with plastics while the extrusion process can deal with plastic and metal materials.
Is the extrusion process fast?
Extrusion is an extremely fast metal forming process. Non-ferrous alloys can be extruded between 1/2 inch per second and 6 inches per second. The extrusion speed ultimately depends on the machinery being used.
What metals can you extrude?
Aluminum, brass, bronze, copper, magnesium, steel, stainless steel, titanium, and zinc. Plastic materials can also be extruded via the plastic extrusion process.
What are plastic extrusions used for?
Some common uses for plastic extrusions include decorative trims, custom plastic containers, and other plastic items like display racks.
Does the die entry angle effect the extruded part?
Yes, the die entry angle has distinct effects on the mechanical properties of an extruded part.
Extrusion Conclusion
Extrusion stands as a foundational manufacturing process with a remarkable impact across diverse industries. Its versatility, precision, and efficiency make it an indispensable technique for shaping various raw materials into products that have become integral to our daily lives.
Understanding the mechanics and applications of extrusion sheds light on its significance in modern manufacturing. As technology advances and the need for sustainable manufacturing processes grows, the evolution of metal extrusion processes will likely continue, contributing to a more efficient, innovative, and environmentally conscious industrial landscape.
Start a Custom Metal Extrusion Project With the Federal Group USA Today
The Federal Group USA is a leading manufacturer in the world of custom metal extrusion. Whether your product requires hot extrusion, cold extrusion, direct extrusion, or indirect extrusion, we can handle your requirements.
Contact us today to speak with a sales engineer regarding your next extrusion project.